Farbunterschiede: Ursachen und Lösungen für Designer
Autorin: Sophie Chen
Datum: 14. November 2024
Im vorigen Artikel haben wir die Herausforderungen des Stoffmusterdesigns vom Konzept bis zur Produktion erörtert. Diejenigen, die mehr über Musterdesign erfahren möchten, können auf diesen Link klicken, um ihn anzusehenhttps://blog.docsunhomeandliving.com/the-vast-gap-between-design-concepts-and-production-results-exploring-the-challenges-and-adaptability-in-fabric-pattern-design/. Jetzt wollen wir uns darauf konzentrieren, die Lösungen zu analysieren, die Designer verwenden, wenn Farbunterschiede auftreten, ein häufiges Problem, das während des Prozesses für kundenspezifische Produkte auftritt. Tauchen wir ein und erkunden wir es.
Da Seidenschals zu einem beliebten Modeaccessoire geworden sind, hat die Anpassungsfähigkeit ihres Designs und ihres Produktionsprozesses immer mehr Aufmerksamkeit erregt, insbesondere mit der steigenden Nachfrage nach personalisierten Designs. Von Luxusmarken wie Hermes, die auf innovative Schal-Designs drängen, bis hin zu modernen Designern, die individuelle Anpassungen erforschen, spiegelt das Musterdesign nicht nur die Markenkultur wider, sondern trägt auch den ästhetischen Wert der Produkte.
In diesem Artikel untersuchen wir den "Albtraum eines zwanghaften Designers" - wie Farbunterschiede (Farbvariationen) entstehen und wie man sie beheben kann. Wenn Sie mehr über mögliche Probleme vom Entwurf bis zur Produktion erfahren möchten, lesen Sie bitte Die große Kluft zwischen Designkonzept und Produktionsergebnissen: Erforschung der Herausforderungen und Anpassungsfähigkeit in Gewebemuster Gestaltung.
1.. Farbunterschiede sind ein häufiges Problem
Die Ausprägung von Farben wird durch eine Vielzahl von Faktoren beeinflusst, darunter die Umgebung, Farbstoffe und Produktionschargen, was bedeutet, dass die Farben des entworfenen Musters nicht immer mit den Farben des fertigen Seidenschals übereinstimmen.
Ich habe einmal zwei Muster identischer schwarzer Kissenbezüge erhalten - einer war schwarz mit einem Hauch von Blau, der andere schwarz mit einem Hauch von Rot. Der Grund dafür war, dass der Hersteller verschiedene Chargen von schwarzem Stoff verwendet hatte und die Farbstoffe aus diesen Chargen leichte Farbunterschiede aufwiesen. Dies ist ein häufiges Problem. Selbst bei ein und derselben Stoffpartie können ungleichmäßige Farbverläufe sowie Spannungsunterschiede während der Produktion zu Farbunterschieden zwischen der Mitte und den Rändern des Stoffes führen. Farbunterschiede sind eines der häufigsten Qualitätsprobleme bei der Herstellung von Seidenschals und haben die Designer dazu veranlasst, ihre Entwürfe wiederholt anzupassen.
2. Die Ursachen für Farbunterschiede erstrecken sich über den gesamten Design- und Produktionsprozess
1) Inkonsistentes Farbmanagement zwischen Design- und Produktionsabteilungen
Ein Mangel an standardisierten Farbmanagementsystemen zwischen den Abteilungen führt oft zu willkürlichen Farbentscheidungen, die nicht einem einheitlichen Farbstandard entsprechen. Selbst wenn Pantone als Standard verwendet wird, können Abweichungen zwischen verschiedenen Pantone-Versionen immer noch zu Diskrepanzen führen. So können beispielsweise Pantone-Farbnummern mit unterschiedlicher Reihenfolge dazu führen, dass die Design- und Produktionsteams unterschiedliche Farben erhalten.
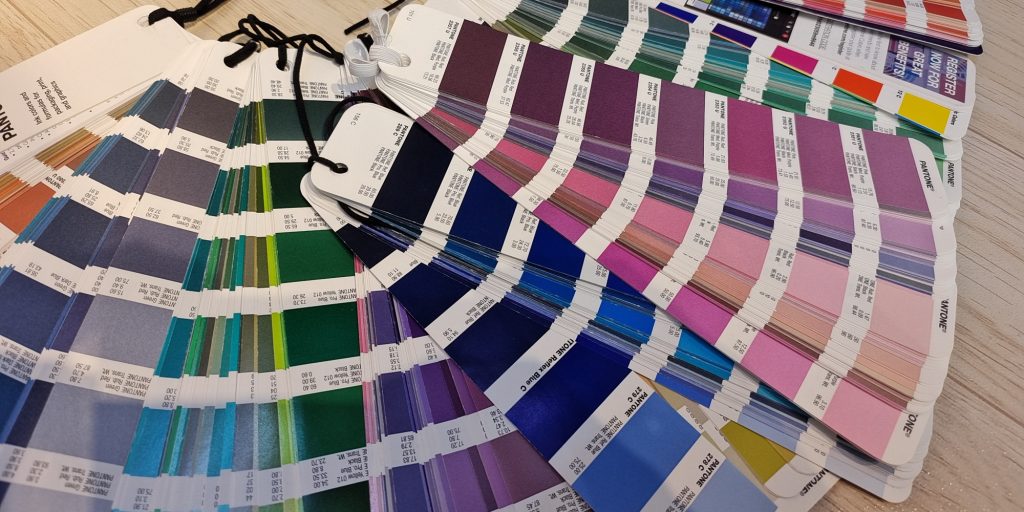
2)RGB- und CMYK-induzierte Farbunterschiede
Designer verwenden häufig den RGB-Farbmodus in Photoshop, um Farben auszuwählen, während der industrielle Druck das CMYK-Farbmodell verwendet. Diese beiden Modi unterscheiden sich in Sättigung, Helligkeit und Farbton, was zu Abweichungen führt, wenn das Design in die Produktion übertragen wird.
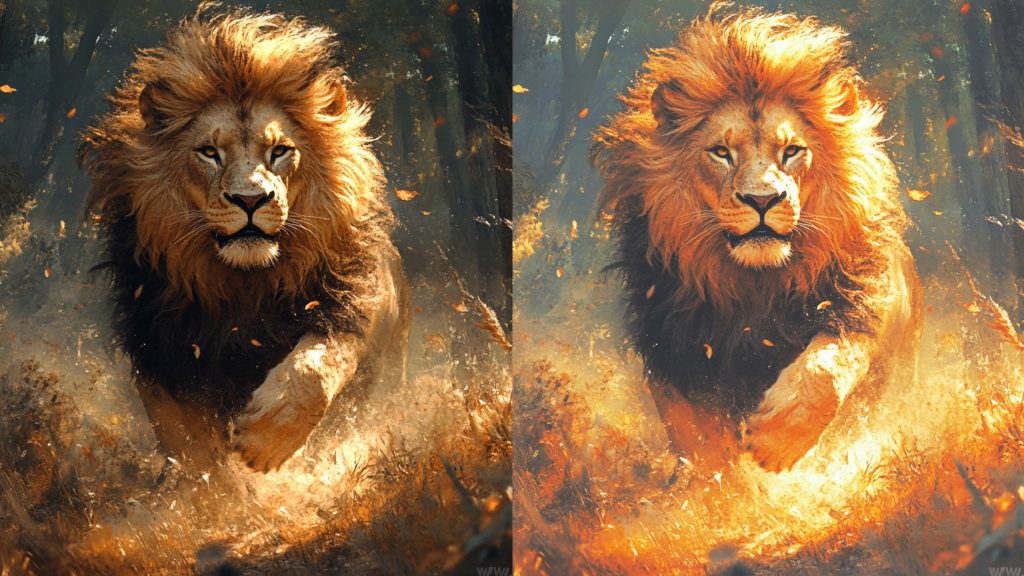
3)Dateispeicherung, Komprimierung und Formatkonvertierung
Beim Speichern, Komprimieren oder Konvertieren von Designdateien kann es zu Datenverlusten kommen, die die Farben verändern können.
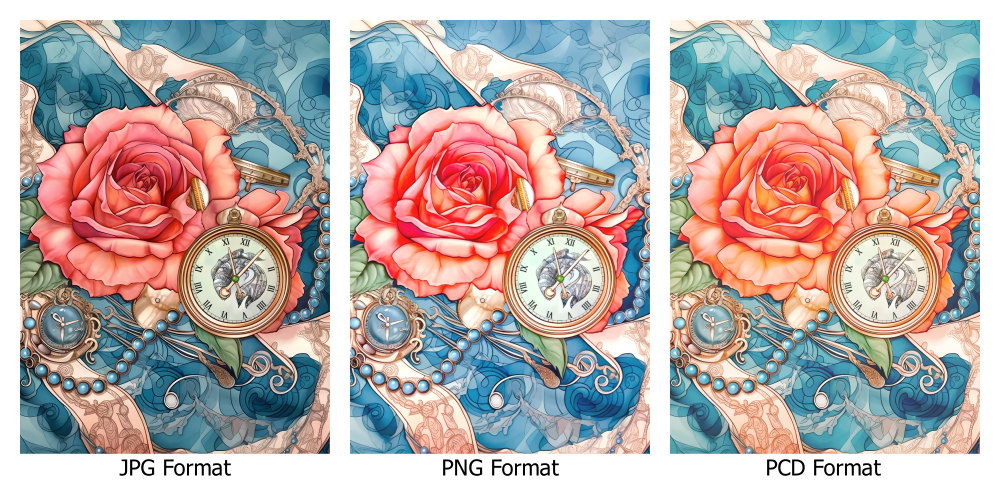
4)Geräteinduzierte Farbunterschiede
Verschiedene Monitore können Farben unterschiedlich darstellen, und wenn die Entwürfe vom Bildschirm auf die Druckmaschine übertragen werden, können inhärente Unterschiede zwischen den Geräten zu Farbabweichungen führen. Ein sorgfältiger Ansatz erfordert die Kalibrierung aller Geräte - vom Monitor bis zum Drucker -, damit die Farben übereinstimmen. Wenn diese Kalibrierung nicht regelmäßig durchgeführt wird, kommt es im Laufe der Zeit zu einer allmählichen Abweichung der Geräte und damit zu merklichen Farbunterschieden.
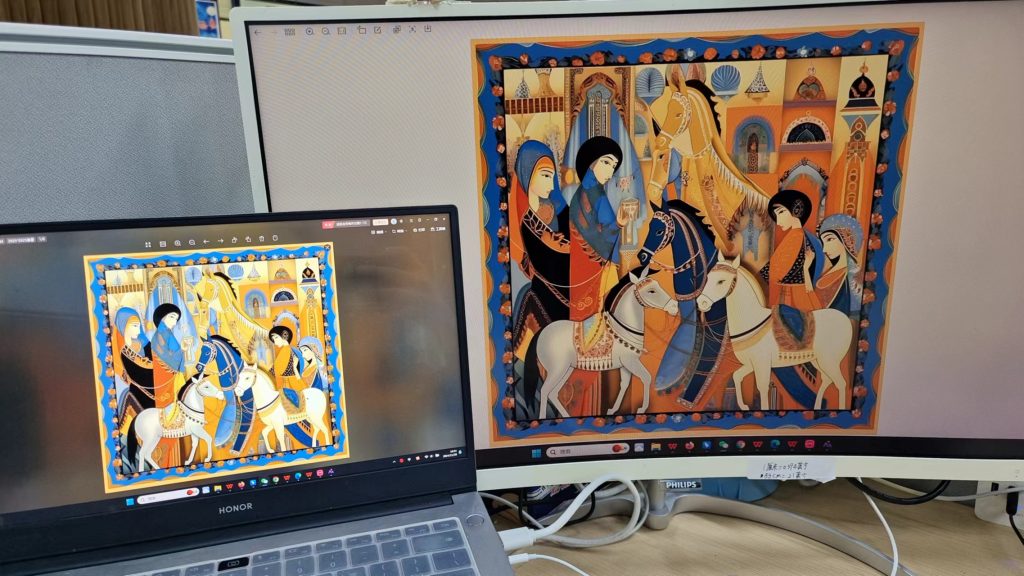
5)Die Rolle des Auges und der Vorlieben des Siebdruckers
Für hochwertige Schals mit satten, leuchtenden Farben wird immer noch der Siebdruck anstelle des Digitaldrucks verwendet. Dabei müssen Coloristen die Farben manuell mischen. Für luxuriöse Schals wird in der Regel ein High-End-Drucker benötigt, der ein farbgenaues Muster herstellt, das dann vom Koloristen zur Anpassung der Produktionsfarben verwendet wird.
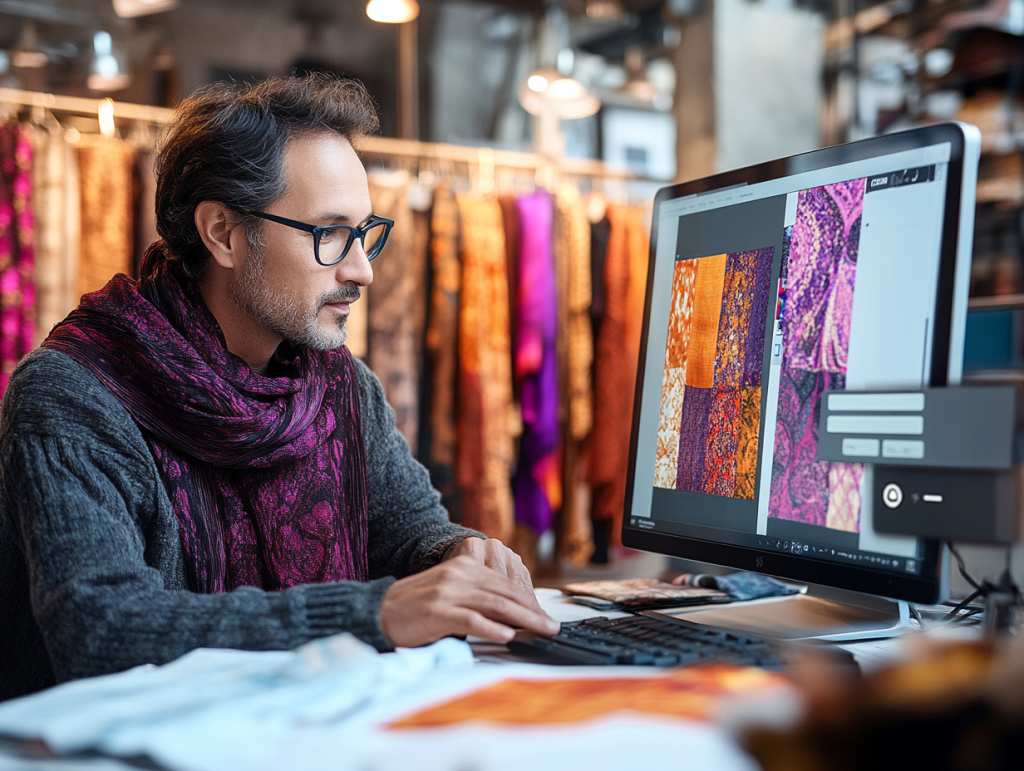
6)Produktionsprozess-bedingte Farbunterschiede
Während frühere Stadien (Design und Vorproduktion) zu Diskrepanzen führen können, kann auch der eigentliche Produktionsprozess weitere Probleme mit sich bringen. Unterschiede in der Qualität der Färbepartie, der Färbetechnik, der Absorptionsrate des Stoffes, dem Waschen nach dem Färben, der Formgebung und der Trocknung können zu Farbunterschieden führen.
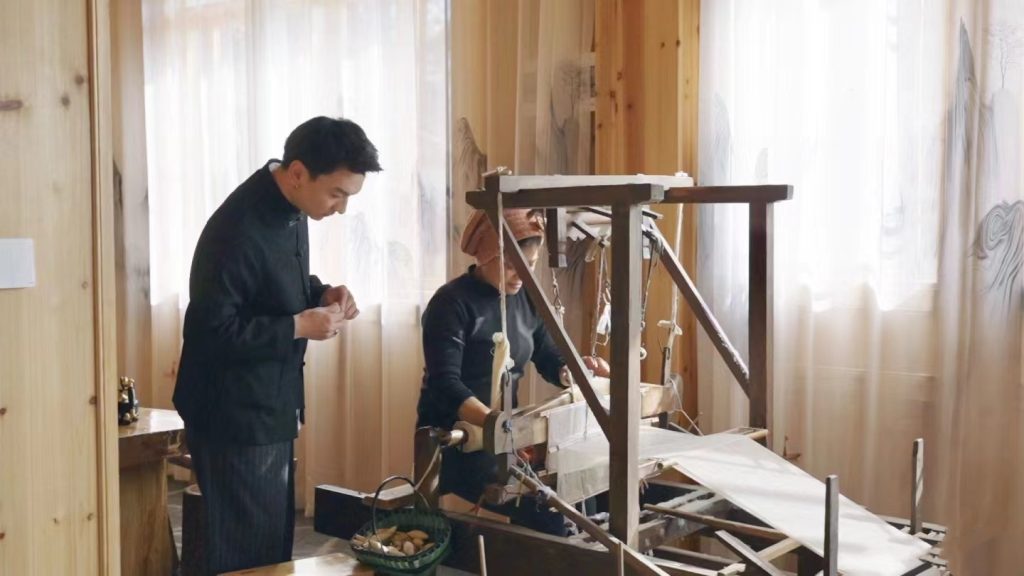
Farbunterschiede beeinträchtigen nicht nur das Aussehen des Produkts, sondern können auch zu Unzufriedenheit beim Verbraucher führen. Besonders problematisch ist dies bei der Massenproduktion, wo Unterschiede von Charge zu Charge dazu führen können, dass das gleiche Design in leicht unterschiedlichen Farbtönen erscheint, was das Image der Marke beeinträchtigt. Um negative Auswirkungen auf die Produktqualität zu vermeiden, müssen Designer für Farbstandardisierung und -konsistenz sorgen. Hersteller können Farbunterschiede verringern, indem sie Faktoren wie Temperatur, Feuchtigkeit und Farbstoffkonzentration während der Produktion streng kontrollieren.
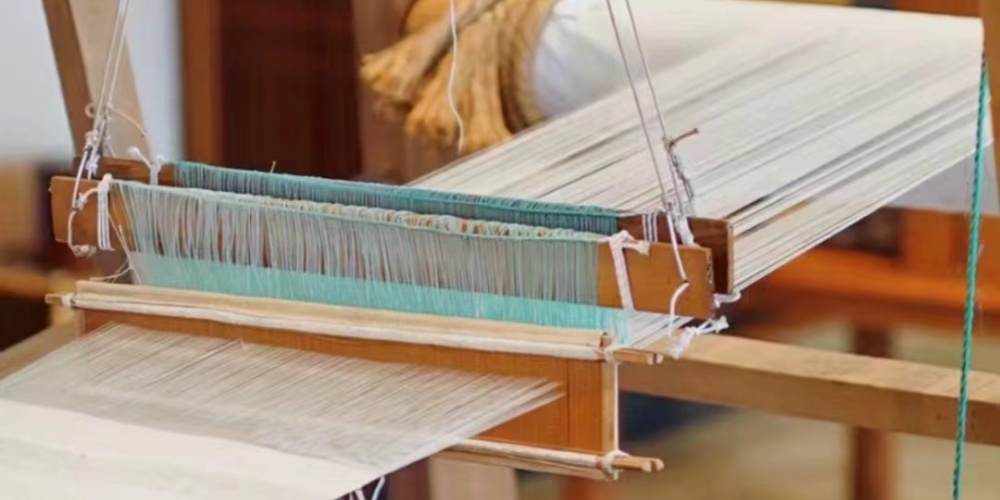
Lösung
Um diese Probleme zu lösen, müssen Sie einen zuverlässigen Hersteller und Designer finden. In der Regel handelt es sich bei denjenigen, die Farbunterschiede wirksam kontrollieren können, um erfahrene Fachleute mit einem umfassenden Verständnis von Farbe, Produktionsprozessen und Maschinen. Außerdem müssen Sie ein gewisses Maß an Farbabweichungen klar erkennen und akzeptieren. So vermeiden Sie, dass Sie sich zu sehr auf eine perfekte Farbgenauigkeit fixieren, was den Prozess wesentlich reibungsloser macht.
Wenn Sie mehr über den Stoff, die Handwerkskunst, den Herstellungsprozess erfahren möchten oder eine weitere Zusammenarbeit wünschen, senden Sie uns bitte eine E-Mail über die folgende Adresse vip@docsunhomeandliving.com, oder klicken Sie auf das Bild unten, um unsere offizielle Website zu besuchen. Sie können auch besuchen Docsun Seide für die tägliche Outfitberatung.
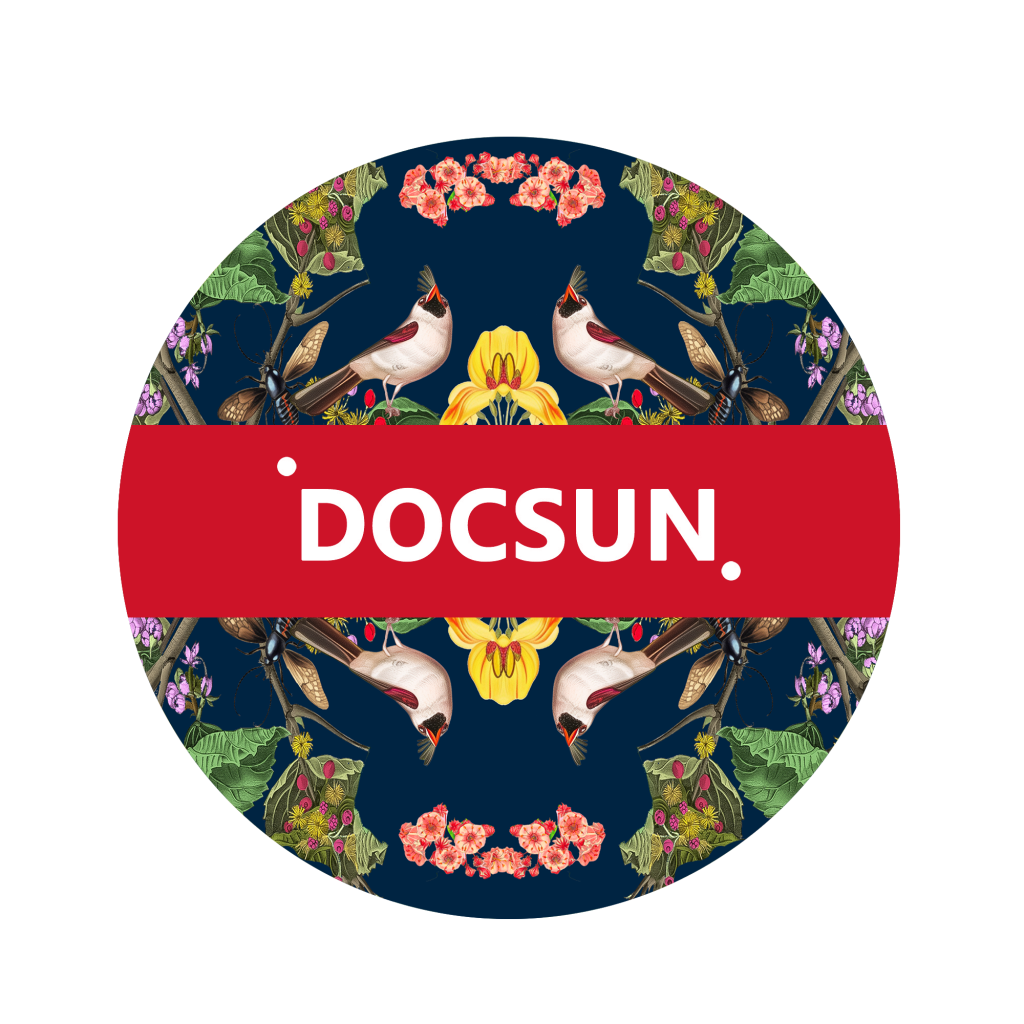